Retyre is a UK-based tyre recycling technology using Ultra High Pressure Water jetting to strip rubber from end of life tyres; Dr Geoff Fowler has carried out extensive research into the process and the material produced
End of life car tyres have long been recognised to be a major global waste problem, with reportedly more waste tyres on the planet than people. Mechanical shredding and granulation of ELTs are well-established practices, enabling the recovery and reuse of their rubber. This rubber is added to masterbatches in limited quantities (typically less than 20 per cent) because it lacks the same properties as virgin rubber, meaning it is only used in low-grade applications such as road furniture, speed humps or as a filler in non-critical products. It has also seen widespread use in building products, roads, playground surfaces and such like. Recent EU rulings mean that tyre granulate of <5mm has been classified as a microplastic and banned from playgrounds or sports pitches due to health and toxicity concerns from chemicals in the rubber.
The most common methods of granulating rubber use well established technologies that rely upon applying cutting, tearing and abrasive mechanical forces at ambient temperatures, to reduce the whole tyre to manageable pieces and extract the steel. Although the rubber particle sizes achieved are within the desired ranges for current uses, they have been chemically modified. The energy from the machines and process is transferred to the rubber causing molecular-level changes to the rubber particles, meaning that they do not have the same chemical properties as virgin rubber. This limits their reuse.
New innovations and outlets for the recovery and reuse of rubber from ELTs are essential to ensure that this significant resource can be reused, in a way which not only conserves resources, but also gives an opportunity for fully valorising this material and safeguard its availability for future generations. Burning the rubber for heat or energy, which is increasingly being seen as the only alternative, goes against the circular economy model and is the lowest value process and is environmentally very damaging.
A novel solution and product
ReTyre Ltd, based in the UK, building on research from Imperial College London funded by Innovate UK, have invented a machine which provides a means of separating the constituent components in car ELT (Steel, fibre and rubber) and produces a <500 micron rubber powder in a single-step micronisation process. The micronisation technology uses no chemicals, only water travelling at supersonic speed.
The water-micronised rubber powder has unique surface morphology, compared to mechanically ground rubber. The images below show this difference very clearly.
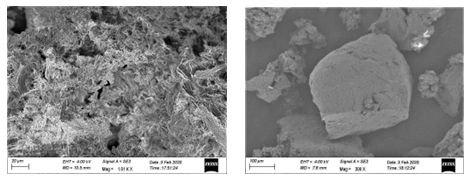
The surface morphology of the water-micronised rubber is markedly different from the mechanically produced material. The complex texture of the water-micronised product is considered to be one of the reasons why this rubber is superior in its performance in new rubber mixes.
The holy grail for rubber recycling is to enable rubber to be reused in a completely circular manner, passing from product to product and not degrading or losing its basic properties. material. This proprietary material, “Activ-R”® has significantly different properties which make it far superior to mechanically made rubber granulates. The ReTyre process has made a significant step towards achieving this goal by recovering a material from ELTs which can be added back into new rubber formulations. In-rubber testing was undertaken using the micronised rubber at 35% w/w in a rubber mix. The range of particle sizes tested and selected results are provided in the table below. The results from the TS2 testing are particularly interesting as they show that the rubber mixes underwent reaction very quickly. This indicated an exceptionally high surface activity for this particular particle size range.
Test | Standard | Units | Control | 50 -150 | 140 – 400 | >400 |
Rheometer 30mins@ 160°C | BSISO 6502:2018 | |||||
TS2 (time to vulcanization) | m:s | 2:05 | 2:20 | 0:16 | 0:14 | |
TC50 (50% crosslinked) | m:s | 4:59 | 4:58 | 3:26 | 3:26 | |
TC95 (95% crosslinked) | m:s | 21:11 | 22:18 | 20:45 | 21:26 | |
Mooney Viscosity ML(1+4)@1oo·c | MV | 105.5 | 182.5 | 179.5 | 181 | |
Hardness | BS-ISO 48-2: 2018 | IRHD | 83 | 79 | 78 | 78 |
Tensile Strength | BS ISO 37:2017 | MPa | 14.94 | 14.52 | 14.81 | 13.83 |
100% Modulus | MPa | 2.58 | 2.19 | 2.32 | 2.46 | |
300% Modulus | MPa | 11.35 | 9.61 | 11.06 | 11.08 | |
Elongation@ Break | % | 371 | 410 | 368 | 354 | |
Tear Strenqth | ISO 34-1 : 2015 | N/mm | 41.4 | 36.9 | 37.2 | 37.2 |
Density | BS ISO 2781: 2018 | g/cm3 | 1.1962 | 1.1938 | 1.1925 | 1.1911 |
The key inference of this result are that the water-micronised rubber from ELT has a strong affinity for the rubber matrix and readily reabsorbs and thus bonds into the new rubber network.
The implication for this observation are significant, as it means that, for the first time, rubber can be recovered from end of life tyres that has properties which make it compatible for reuse in new, high quality rubber products and it may be able to be recycled again (and again…).
A further advantage for the ReTyre process is that rubber can be recovered from ELTs in a targeted manner, meaning that tread rubber, side walls and inner liners could be selectively removed and micronised. The benefits of this are significant, as these rubber formulations could then be reused within the same part of a tyre – A truly circular solution.
The Technology set-up
The standard ReTyre system fits into a 40-foot sea container. This dimension makes it perfect for transportation to tyre stock-piles or installation in tyre depots or at larger tyre shops. Micronising the ELTs at point of removal from the vehicle clearly has major benefits in terms of shipping efficiency (an ELT is >80 per cent void space), removing the need for bailing.
The current systems is available to view and order. Through a process of continual improvement, the control systems will be upgraded.