New Zealand’s Tyrewise has announced funding to help develop markets for recycled tyre materials
In a move that exemplifies how recycling fees should be used for the benefit of the industry and the environment, Tyrewise has announced a round of funding to help grow interest in tyre derived materials.
Innovators, investors and change makers are being called on to put their best ideas forward as a substantial investment in funding becomes available to develop the market for tyre-derived recycled rubber material, and create economic value from Aotearoa New Zealand’s worn-out tyres.
Tyrewise is looking for initial expressions of interest in its inaugural grant funding round. Expressions of interest are open in this first round from 1 July to 29 July 2025. Up to $7 million will be available over three rounds in a financial year.
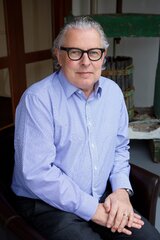
Tyrewise works with the whole industry to ensure tyres are collected for recycling or repurposing. The scheme is achieving a high collection rate and is now focussing on developing high-value, best use recycling and repurposing solutions for the tyres, says Mark Gilbert, Chair of Auto Stewardship New Zealand that governs the Tyrewise scheme.
“To enable this goal, Tyrewise is providing contestable funding to help develop end markets for the recycled rubber material from tyres in New Zealand,” Gilbert says.
Tyrewise has a goal of 80%, of our end-of-life tyres to be recycled and repurposed into new products in New Zealand by its fourth year of operation, and over 90% by its sixth year.
“Tyres are a versatile resource that can be turned into many products or used in a number of processes, such as roading, playground surfacing, as a substitute for aggregate, or even earthquake-proofing buildings. The market in New Zealand isn’t currently big enough though to take all the recycled rubber from tyres which are collected, so the aim of the fund is to stimulate the development of new products and markets here says Adele Rose, Tyrewise Scheme Managers, 3R Group”
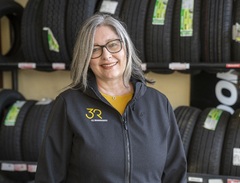
The fund is structured into three main ‘streams’ – research and development, emerging markets, and community development. “This allows funding to back projects across the spectrum of the typical phases of product development,” Rose says.
To be eligible for funding, applicants must be a registered New Zealand business, research institute, or university, ideally have been operating for at least 12 months, and have satisfactory environmental, safety and financial performance, among other criteria.
“This is a call for expressions of interest. Once we have assessed them, we will ask for a more formal, detailed application,” Rose adds. “Kiwis are innovators by nature, so we’re excited to see what ideas are out there to create a circular economy for tyres here at home.”